Comet TraComet Traitements or the art of transforming and recovering wasteitements ou l’art de transformer et valoriser les déchets.
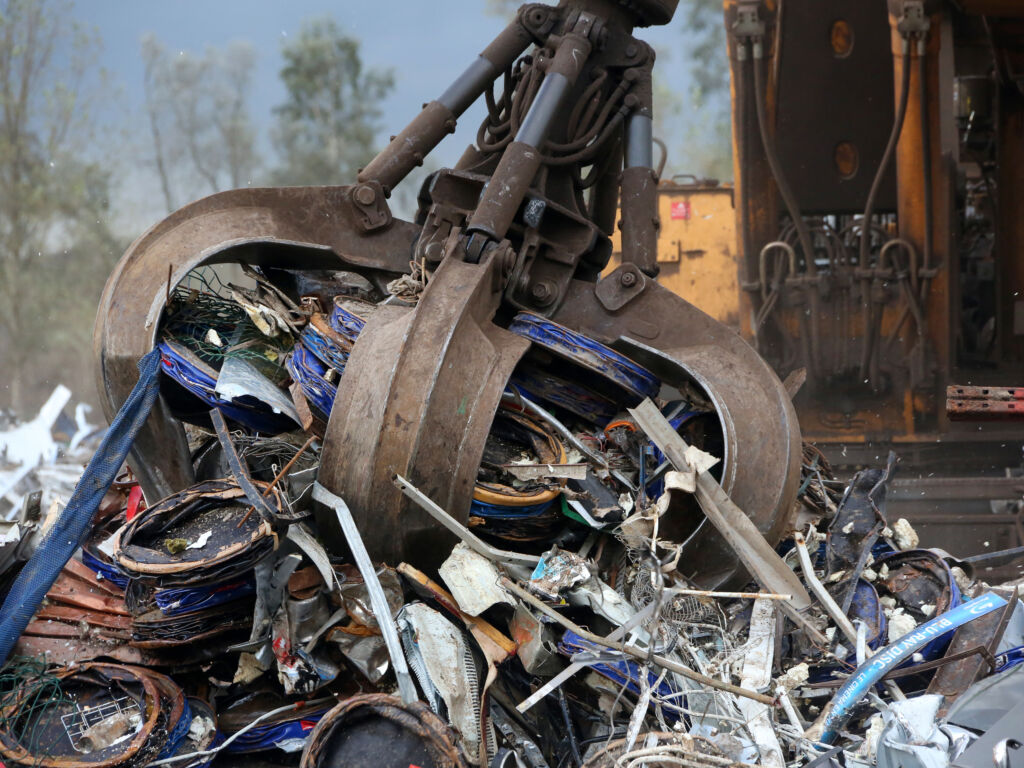
- Member
- Comet Traitement
The recycling and recovery rate for end-of-life vehicles - ELVs for acronym lovers - has reached a ceiling of 95%. Not bad, is it?
For the R&D division of the COMET Group, based in Châtelet and Obourg and specializing in the recycling of ferrous and non-ferrous waste, it couldn't get any better! Their idea for innovation? To use pyrolysis - not the kind used to clean your oven, but not far off - to heat break down the remaining 5% of waste (foam, textiles, rubber, wood, etc.) and transform it into valuable products.
- Ecosystem
-
- Renewable Energy
- Success criteria
-
- Production or business model transformation
- Sales revenue inscrease
- Job creation
- Long-term innovation
- International development
- Disruptive innovation
An innovative 100% Walloon project
The PHOENIX project in Wallonia combines the skills of COMET Traitements with those of the Certech, CRM and ULiège research bodies, as well as those of Slegten. This 100% Walloon consortium has created a unique industrial process for recovering waste that was previously untreatable. The overall rate of ELVs recycled by COMET is now 98.4%, making the company a pioneer in ELV recycling and recovery in Europe.
The Comet Group was founded by Alfred Grosjean, who brought together various scrap metal collection sites in Hainaut and Northern France. Since then, the group has continued to develop and diversify its activities. Today, Comet operates around thirty sites in France and Belgium and employs 500 people.
The Comet Traitements adventure began in 2002. Its mission was to find a destination for end-of-life shredder residues. The development of the PHOENIX project led to the construction of a pilot site at Obourg, which was inaugurated on 11 November 2013. ‘This is a unique solution in Europe. Our aim, once this first plant is up and running, is to market the technology,’ says Pierre-François Bareel, an engineer by training and CEO of Comet Traitements.
Comet Traitements transforms waste into liquid gold
Phoenix is now being expanded by ‘Phoebus’, a unit installed in 2017. The fuel obtained after treatment in the Phoebus pilot unit feeds cogeneration engines that simultaneously produce electricity and heat.
The combined capacity of these two facilities is to produce around 1,000 litres/day of synthetic diesel and petrol.
This is an important step in the development of this technology, the aim of which is to be able to implement an industrial facility with a capacity of 35,000 t/year of shredder residue and produce the equivalent of the electricity consumption of 10,000 Walloon households.
This fuel emits the same amount of CO2 as normal oil, with the added advantage of giving a second life to very bulky organic matter that would otherwise have ended up in a landfill.
The MecaTech cluster: turning innovative ideas into reality
Just as you turn to a financial institution and a good architect for your personal projects, innovative manufacturing companies like COMET turn to the MecaTech cluster to build their innovation project, team up with high added-value partners and secure the best possible funding.
85% of projects supported by the MecaTech cluster obtain funding
This is the case for the Phoenix project, which has benefited from project set-up assistance and, consequently, a major financial boost from the Walloon Region, to the tune of €4,554,000 out of a total amount of €7,444,000, i.e. more than 60% of the total investment. COMET injected €3.25 million of this amount into the manufacture of the industrial pyrolysis equipment. This additional activity within Comet's recycling park has led to the creation of new jobs and business opportunities in Belgium and Europe.
We've gone from being scrap metal dealers to experts in the circular economy
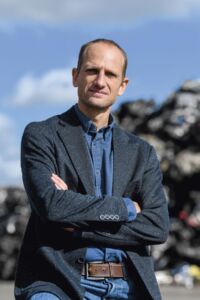